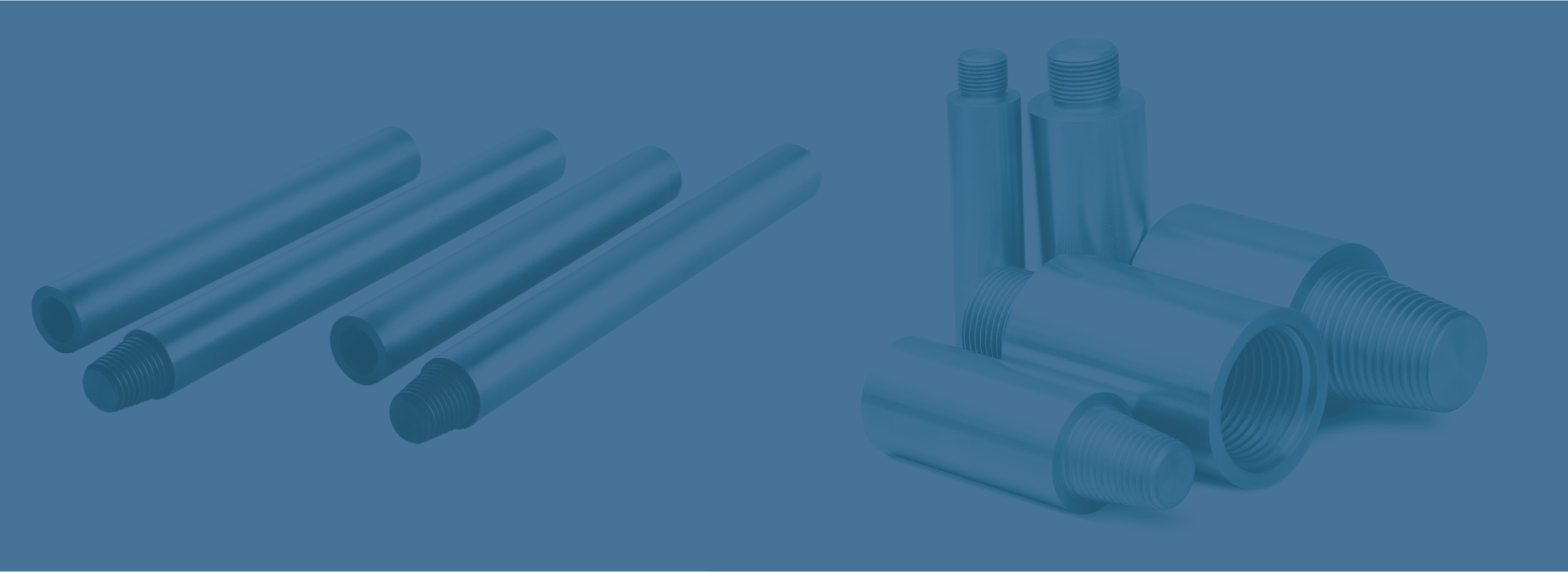
About Glass Melting Electrodes
Glass melting electrodes are resistance heating elements that pass electric current through them to generate heat within molten glass. Also known within the industry as GMEs, these critical components support various glass melting processes. GMEs assist in the production of food and beverage containers, fiberglass and insulation materials, glass for the solar industry, tableware and more.
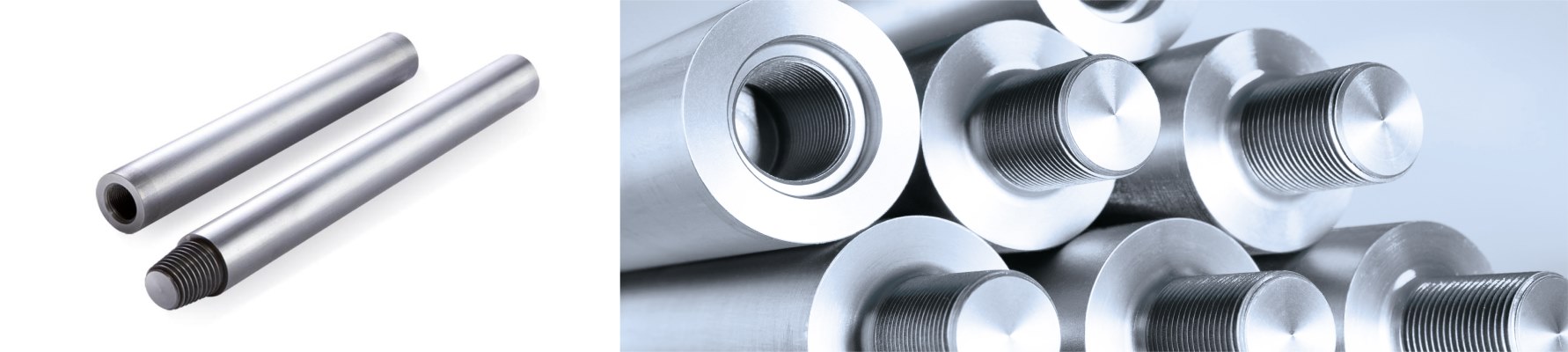
Elmet Technologies manufactures a comprehensive line of advanced glass melting electrodes. Our process starts with our very own high purity molybdenum powder. Electrodes are available in various dimensions. We offer various standard and custom threading options to meet precise customer requirements. Other features include oxidation-resistant coatings to further protect the electrodes.
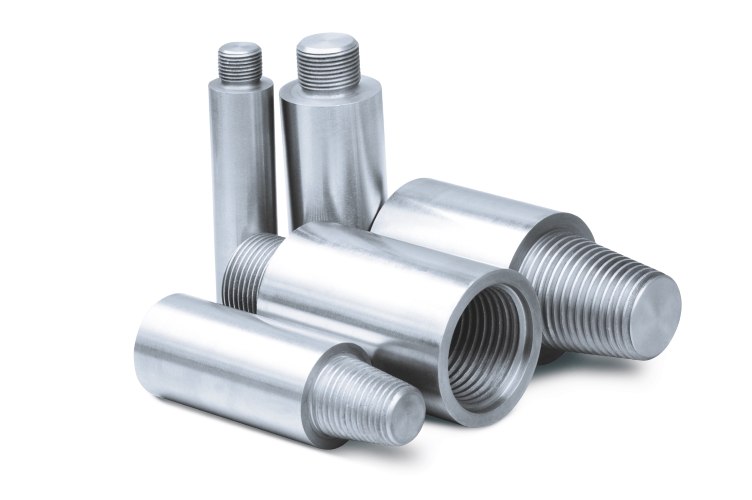
Electrodes: About The Materials
Material selection for glass melting electrodes includes: high-purity molybdenum (Mo, 99.95%), and premium molybdenum zirconium (MoZrO2). While molybdenum remains the material of choice for electric-boost, gas-fired furnaces, it is occasionally alloyed with small amounts of zirconium to improve corrosion resistance. To further improve the material, advanced coatings may be employed, allowing the glass melting electrodes to be brought up to temperature in air without oxidation.
Glass Melting Electrodes: Types
- Powder metallurgy based: The most common and economical method of manufacture. Proven stability across most furnaces and glass types.
- Electron beam melted: Highest degree of product consistency and performance. Used for premium glass where chemistry control is paramount.
- Zirconium doped Mo electrodes: Improved molten glass contact corrosion and increased strength at elevated temperatures. Confidence for glass melting electrode use with more aggressive molten glass environments.
- Coated Mo electrodes for oxidation protection: Extremely adherent (chemically bonded) ceramic coatings designed to protect the Mo electrode from oxidizing in air, flames, oxidizing chemicals and in general, oxygen rich atmospheres. Mostly used in glass furnace starting. Silica-based, no coloration or other negative effects on the glass.
Glass Melting Electrode Examples
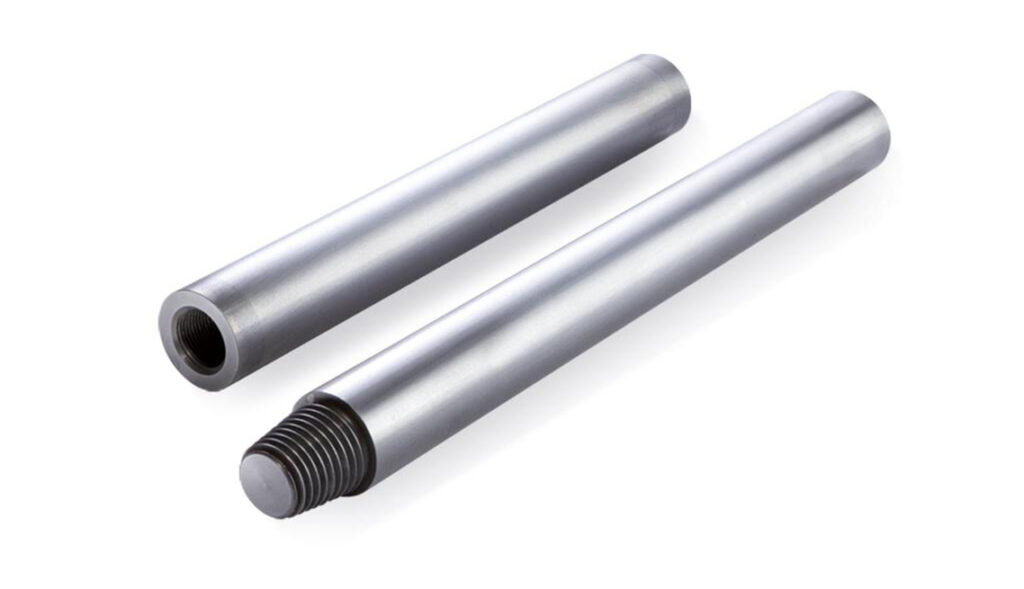
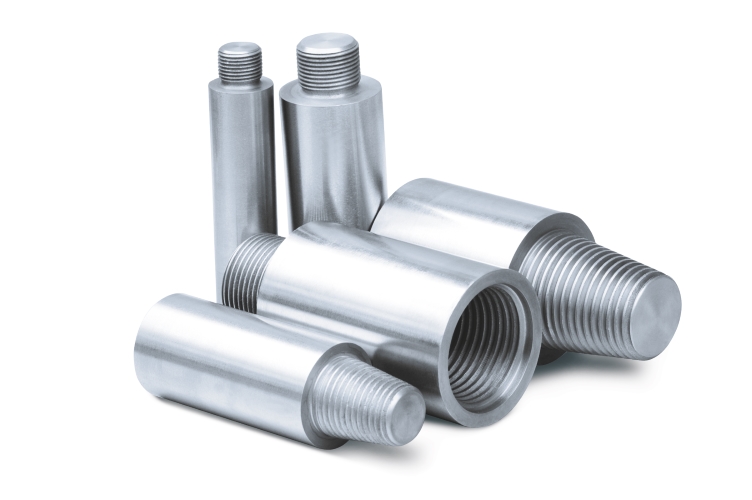
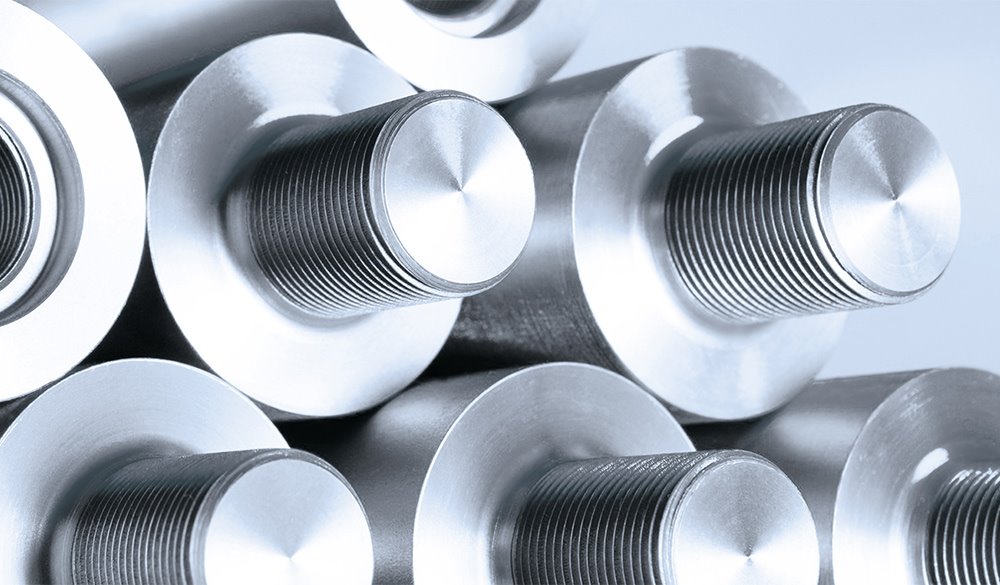
Where do Electrodes Function in the Glass Melting Process?
In the glass production process, electrodes function within glass melting furnaces. For modern processes and applications, glass melting electrodes primarily exist in electric-boost, gas-fired furnaces. Depending on the furnace type, electrodes can assist in the production of a wide range of products, such as: containers, tableware, fiberglass, and glass for the food and beverage industry.
The Key Advantages of Electrodes
- Higher energy efficiency
- More control over operations
- Lower capital cost/unit of capacity
- Less dependence on radiant heating
- More flexibility in meeting environmental emissions
- Lower maintenance costs than alternate heat sources
Factors to Consider For Optimization and Extending Lifespan
There are various mechanisms that may reduce an electrode’s lifespan, causing premature failures or other undesirable effects. Below, we have arranged factors to be aware of, and tips for optimization and extending the lifespan of a glass melting electrode.
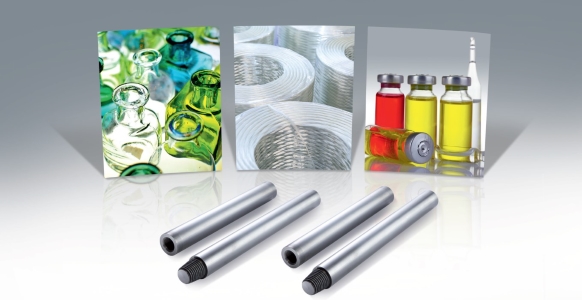
1. Effect of the electrode holder
Improper electrode adjustment in the holder can lead to a very rapid attack of Mo through diffusion of iron, nickel or other elements from the holder into the molybdenum, lowering the melting point of the GME.
2. Contamination of foreign material
Foreign material from outside the furnace can contaminate the electrode. This may reduce its effectiveness and overall lifetime. Extra care needs to be taken to ensure the electrode remains clean during storage, handling, and installation. In addition, the equipment itself must be properly conditioned prior to electrode installation. This will eliminate sharp edges or foreign material.
3. Degradation by air outside the furnace
Molybdenum GMEs start degrading in air at temperatures above 400°C. The oxidation is more intense as temperatures increase with formation of the volatile MoO3 above ~700°C, which leads to rapid loss of metal.
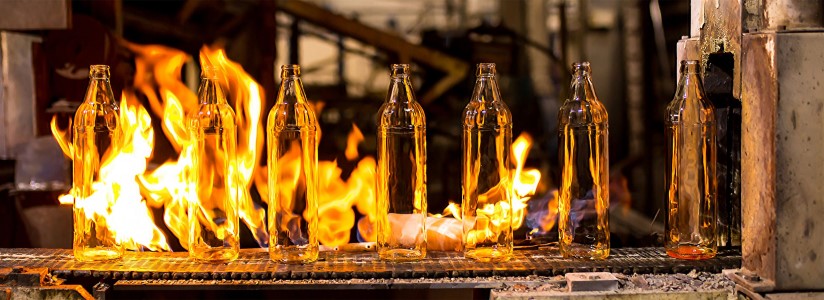
4. Effect of glass chemistry
Elements like lead, chromium, nickel, iron, nitrates, antimony, arsenic, and others present in some types of glass can negatively influence the lifespan of a glass melting electrode.
5. Current density importance in furnace design
Mo GMEs can support a max. of 20A/in2. Higher current densities will lead to a combination of increased electrode surface temperature and increased glass convection. This may ultimately result in excessive electrode erosion. As the electrode’s surface gets smaller with erosion, the current density will further increase. This may eventually lead to complete electrode deterioration.
6. Sagging / creep
Operating at such high temperatures, glass melting electrodes are subject to stresses that make electrodes prone to creep and sagging. Microstructural optimization and control help avoiding sagging under normal operating conditions.
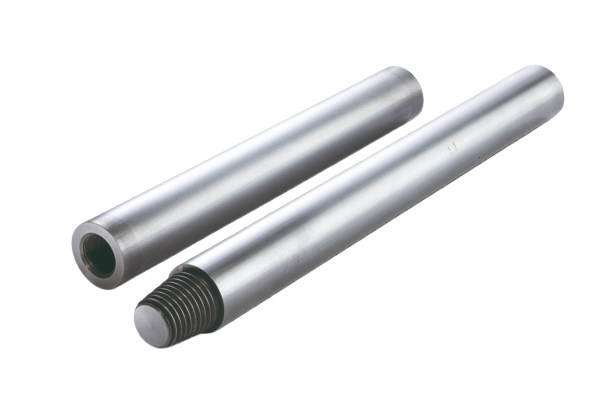
SUMMARY
Overall, proper understanding of factors that negatively impact glass melting electrodes lifespan can have a significant positive impact on the lifetime of GMEs, and, in turn, the overall cost of ownership of glass melting furnaces.
Choosing the Right Type of GME
- Low carbon electrodes for specialty glass
- Straightness for uniform contact with electrode holders
- Controlled chemistry with a purity minimum of 99.95% Mo
- Standard vs. tapered threads (connect and seat 3-4x faster)
- Concentricity: an important factor to ensure proper electrode lifetime
- Controlled microstructure with uniform recrystallized grains for creep resistance
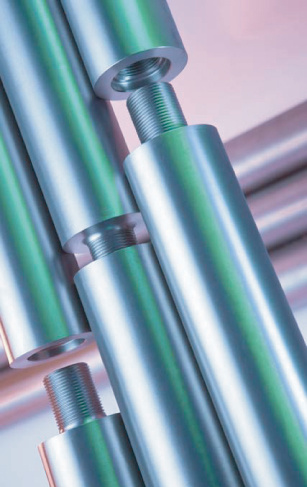