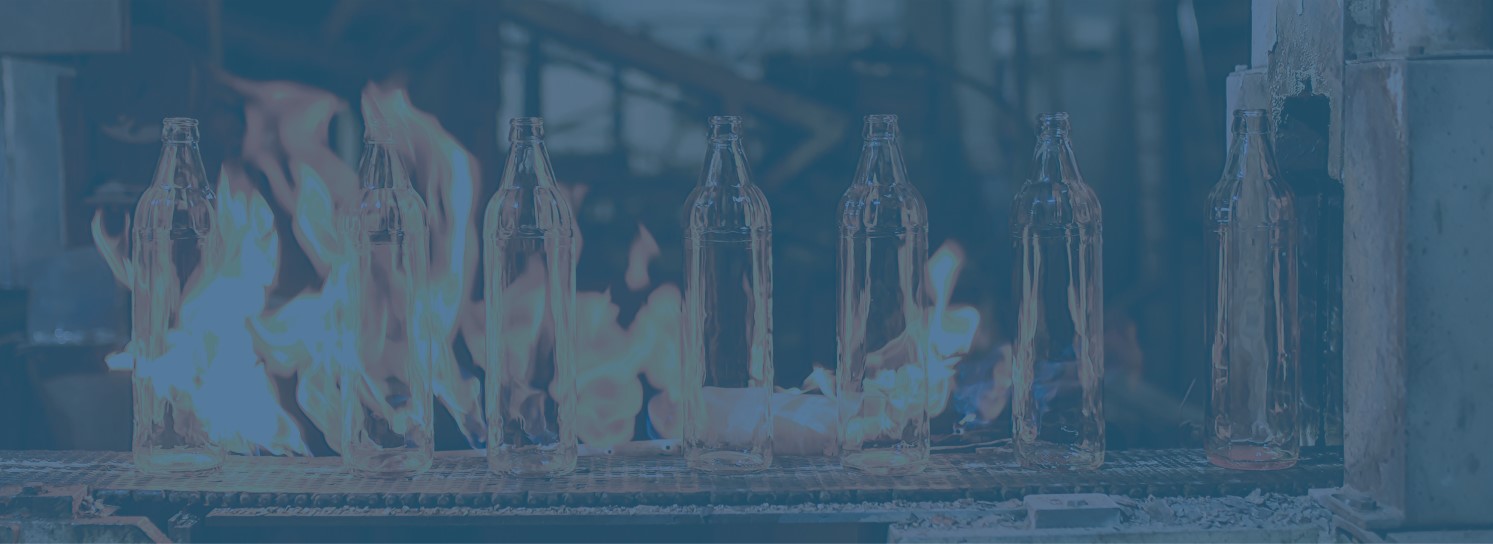
why use Molybdenum for Glass Melting Electrodes?
Molybdenum is the best material for glass melting electrodes because it offers heat resistance, corrosion resistance, and high electrical conductivity. For the electric-boost furnaces and gas-fired operations of today, molybdenum remains the material of choice.
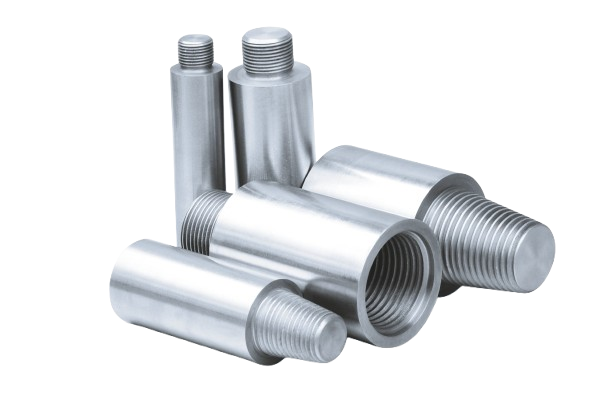
Given the exposure to aggressive chemical conditions and extremely high temperatures, molybdenum is the ideal material for glass melting electrodes (GMEs). Many other materials have limited use due to fragility and low strength at required temperatures.
Molybdenum (Mo) offers unique advantages for its electrical, mechanical, thermal, and non-corrosive properties. These factors are a large part of the reason why molybdenum is the best material for GMEs, making it the de facto standard material for GMEs.
Resource center
DATA SHEETS
Pure Mo Glass Melting Electrodes
BROCHURES
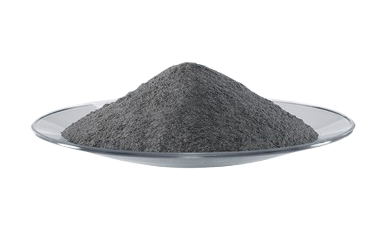
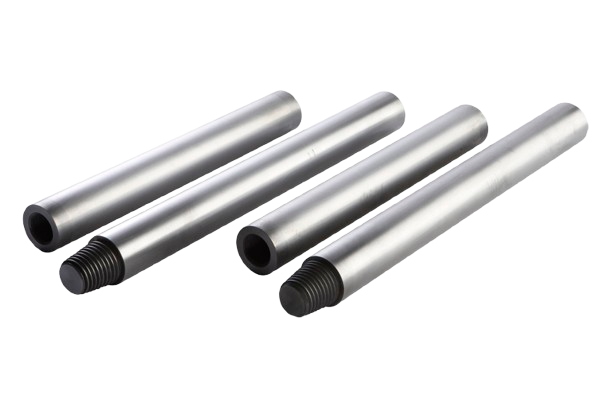
molybdenum material advantages
Molybdenum is the best material choice for electric heating in the glass melting process. It exhibits excellent properties for most glass melts, including the following advantages:
- High thermal and electrical conductivity
- Low coefficient of thermal expansion (CTE)
- Resistance to corrosion
- Minimizes detrimental glass discoloring
- Good machinability
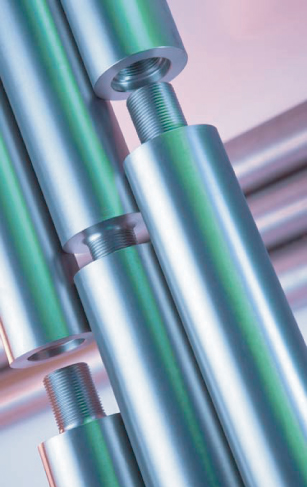
A Brief History of Molybdenum GMEs
In the 1950s, researchers discovered that molten glass conducts electricity. This led to the development of electric furnaces, where heat could be supplied to the molten glass by passing an electric current through it via electrodes submerged in the melt.
Subsequently, molybdenum was ideal for early electric furnaces, exhibiting the required combination of heat resistance, corrosion resistance, and high electrical conductivity (2×10⁻⁷ S/m). Other materials, such as platinum, tin oxide, carbon, and nickel alloys like Inconel have since founded limited use, because these materials suffer from fragility and low strength at the required temperature.
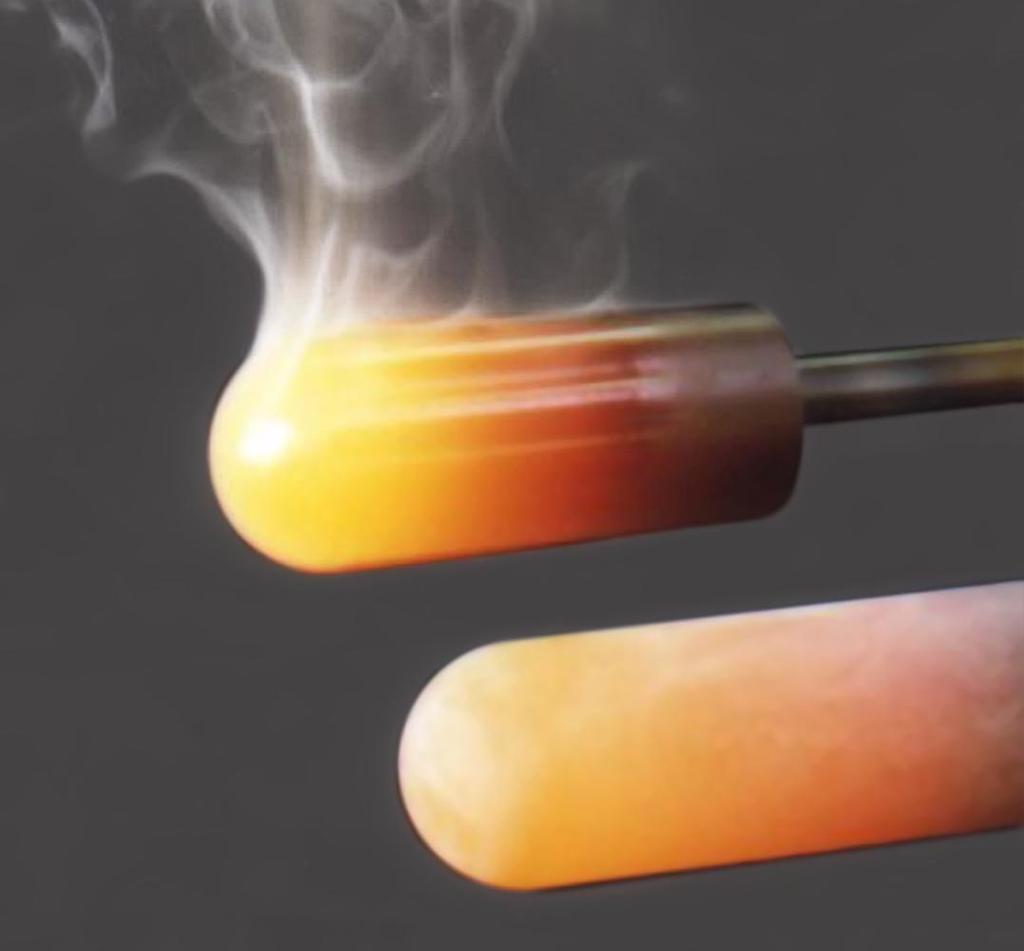
Since GMEs are exposed to extremely high temperatures and aggressive chemical conditions, Mo remains the material of choice for electric-boost and gas-fired furnaces. It is occasionally alloyed with a small amount of zirconium to improve corrosion resistance.
The latest developments for GMEs, including advanced coatings, can even enable molybdenum-based materials to be brought up to temperature in air without oxidation. Elmet Technologies remains at the forefront, developing the next generation of GME solutions.
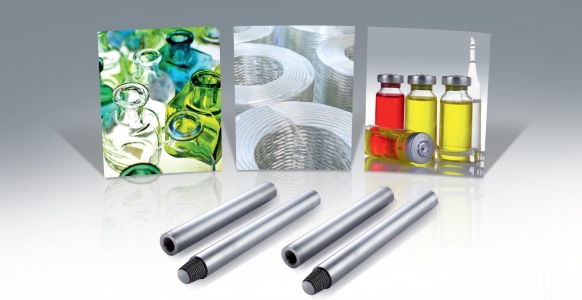
features
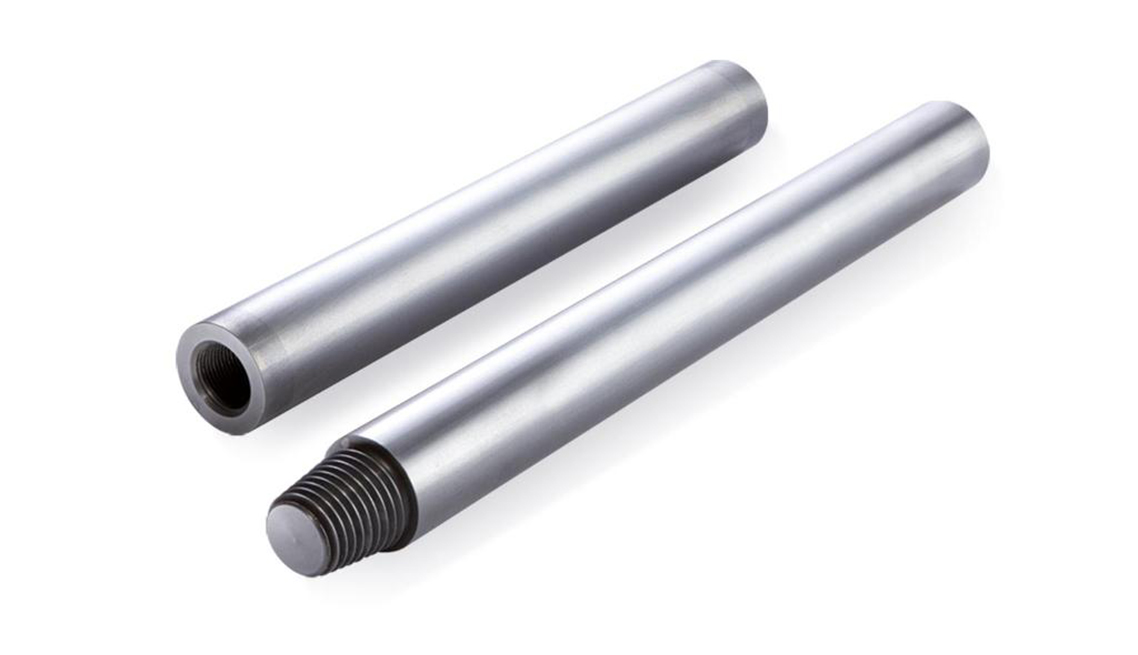
- Uniform recrystallized grains, crucial for enhancing creep resistance
- Available coated and uncoated, with options for conventional or tapered threads
- U.S. and European options in sizes from 1.25 in (32 mm) to 8 in (203 mm) diameter
- Automatic, self-sealing tapered threads allow for a 60% reduction in connect time
- Bubble-free, low carbon electrodes, with exceptional purity level of 99.95% minimum
- Machined or centerless ground surfaces for concentricity and straightness assurance
- Superior oxidation resistant coatings uniformly applied to all surfaces of the electrode
A Global Leader in Refractory Metals
As a worldwide leader in refractory metals, Elmet Technologies has the expertise of working with high performance metals for several applications, including the glass industry. Our team promises outstanding quality, responsive service, and unmatched knowledge for your glass melting purposes.